Innovation has always been a distinguishing characteristic of Murray & Roberts. The company built the world’s first concrete mining headgear and the prestressed concrete version that is commonly used today. It replaced structural steel with concrete in the boiler house structures of thermal power stations, significantly improving their efficiency. Murray & Roberts also established the expertise, design and management capability to meet the stringent demands of the nuclear industry for safety, quality and risk management. Robust explores some of the Group’s latest innovations.
A new era in shaft sinking
Murray & Roberts Cementation is transforming the way mine shafts are sunk in South Africa. The company has been selected by De Beers as the preferred contractor to undertake the development of an underground mining operation at its Venetia Mine and, pending a final feasibility study and the go-ahead from De Beers in 2012, this diamond mine could become the first to benefit from the progressive new methodology.
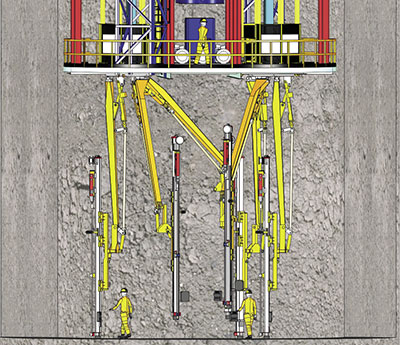
Shaft bottom drilling by means of stage mounted drill rigs.
“We’ve abandoned the traditional South African approach to shaft sinking and the conventional way of carrying out concurrent activities in the sinking cycle,” says Allan Widlake, the company’s business development executive. “All activities in the sinking cycle will be handled in line — no two jobs will happen simultaneously. And, contrary to the assumption that this will slow down the entire cycle, with the full combination of changes we’ve engineered, this approach will actually improve productivities across the board.
“We’ve taken a decision that we will sink no future shafts using traditional South African practices and we have already bid on four new contracts based on the new approach. Two are presently under adjudication and the first shafts will be sunk this way during 2012.”
“The new shaft sinking methodology harnesses sling-down Jumbo’s that nest in the sinking stage. The advantage here is that this equipment can drill a burn cut round, which improves the advance and reduces the fly rock that typically causes damage in the conventional method,” Widlake says. “We’ll use sensitised emulsions for the blast initiation, with vertical shaft muckers housed in the stage — as opposed to cactus grabs. This allows for a faster cleaning time, with only one person needed at the bottom of the shaft during the mucking cycle.
A safer work environment
“There are tremendous safety advantages to this approach, since the muckers are capable of manoeuvring the kibbles into position, eliminating the need for the human element in this dangerous task.”
Murray & Roberts Cementation has also changed the design of the shaft shutter to allow for a six metre lift in a single eight-hour shift. In addition the company has changed the way materials handling takes place on the surface, introducing a more mechanised approach.
ADVANTAGES OF PROGRESSIVE
METHODOLOGY
- Safety – Zero Harm performance
achieved in Canada
- Stronger skill set
- Higher levels of productivity
There has been growing demand from clients, unions and government for improved safety during shaft sinking and for restricted use of certain equipment that has led to accidents in the past. This has provided the impetus for Murray & Roberts Cementation to review and replace the entire methodology in favour of a model tried and tested by sister company, Cementation Canada.
Widlake believes this practice will bring about the same safety statistics currently being recorded by Cementation Canada — a full shaft completed without one Lost Time Injury. This Zero Harm performance is attributable to technology and a higher skills set among the personnel involved.
Murray & Roberts Cementation is converting elements of its world class training facility, Bentley Park near Carletonville to implement components of the skills transfer across all stages of the sinking cycle. Final skills transfer will be conducted on the job, under the supervision of the team’s Canadian counterparts.
Confident of duplicating success
“The scale on which this approach is being applied in Canada and the USA compares favourably with the dimensions of South African shaft sinking requirements and we are confident that we will be able to duplicate its success here,” Widlake says.
“We’re well advanced with the design work to support the transition. We’ve already fully designed the new stages and the new headgear requirements for the sinking phase. All this has been taken to Canada for peer review — the design work, adoption of technology, manpower planning and productivities used — and we have the full endorsement of the Canadian team.” |
A CONCRETE SOLUTION
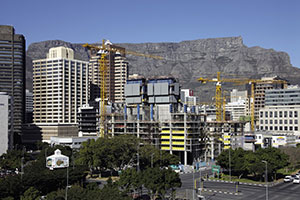
Work underway on the Portside head office for Old Mutual and FirstRand.
When completed, this will be the tallest building in the Cape Town CBD
Concrete is not what it used to be – not since Murray & Roberts scientists set about changing almost everything we thought we knew about this basic building material.
The strength of concrete is measured in megapascals (MPa). In theory, a cubic metre of concrete that is rated 30 MPa (a typical standard for structural concrete) is able to withstand the weight of six bull elephants.
"Smart technology cut cement consumption on the Gautrain Project by about 110 000 tons"
Traditionally, 30 MPa concrete requires between 300kg and 350kg of ordinary cement per cubic metre. But now scientists working for Murray & Roberts have developed a technology that meets the 30 MPa standard using just 25kg of cement or even less. Not only does it meet the standard, it far exceeds it. To date strengths of up to 52 MPa have been achieved using Murray & Roberts’ patented ARC (Advanced Recrystallisation) technology and only 25kg of cement per cubic metre.
Best of all, the ARC process uses large amounts of recycled waste products. The most common recycled ingredient is slag from the steel manufacturing process. However, at the 102 Rivonia Road project, now under construction in Johannesburg, Murray & Roberts Buildings is using up to 64% fly ash, a recycled byproduct from coal-burning power stations for which there is usually no use.
Research scientist, and head of Murray & Roberts’ Concrete Centre for Excellence, Cyril Attwell, says: “Not only does the process require less ordinary cement and is environmentally friendly, but also, because the concrete can gain higher strengths, we can build faster; sometimes a lot faster.”
Cyril, whose official job title is Group Concrete and Research Manager, adds that the typical specification for waste water treatment plants requires concrete that uses 420kg of binder per cubic metre. His team of scientists has now developed techniques that can meet the specification but use only 330kg. “This gives a distinct cost saving advantage to our clients.”
World first technologies that protect the environment
Cyril and his two colleagues at the Concrete Centre for Excellence in Amalgam on the West Rand, Warren McKenzie (Group Concrete Technologist) and Andries Magale (Laboratory Technician) have developed some remarkable concrete technologies, several of which are world firsts. Just one is a smart concrete involving the introduction of a particular type of bacteria into the mix. “Under certain conditions of chemical attack, which are usually bad for the concrete, these bacteria in fact thrive, reproducing rapidly and consuming the chemicals that attack the concrete. In addition, as they eat up the threat, the bacteria defecate calcrete, and these deposits fill up cracks that would normally weaken the structure.”
BENEFITS OF INNOVATION
- Stronger concrete
- Recycling of waste products
- Cost savings
- Protection of marine concrete
The Amalgam team is also investigating an ingenious electrochemical system that makes marine concrete more resilient to both wave action and chemical degradation. The system draws carbon dioxide from the sea water, encouraging the growth of a layer of coral that protects the undersea concrete. Such is the effectiveness of the coral that the concrete doesn’t have to be treated with expensive chemicals – and it is almost completely maintenance-free.
However, such benefits are not just measured in monetary terms. Cape Town’s Portside development, Cyril believes, will be the first building project to receive a full three-star Green Star eco-friendly rating for construction materials. The concrete being poured contains up to 70% waste materials and as much as 10% of the aggregates consumed (typically sand and stone) are waste materials. “Recently the consulting engineer working on Portside asked us to supply even more waste material because it just makes such a strong concrete,” says Cyril. “This technology means we can save money and time, deliver a superior result and, at the same time, do our bit to save the environment.” |
|
A STABLE SEABED FOR BEIRA
Every day the seabed at the port of Beira in Mozambique is shifted by strong tidal forces. The huge propellers and bow thrusters of ships berthing and leaving the port loaded with coal also disturb the seabed.
To address the problems associated with a constantly shifting seabed, port authorities tasked German consultants Odebrecht International to come up with a solution. They turned to Murray & Roberts subsidiary, Technicrete.
The solution designed by Odebrecht and Dutch engineering consultants DHV and executed by Technicrete, involved laying 35 000 concrete blocks assembled into 230 separate “mats” and covering an area of 3 200m² of seabed.
The Armorflex blocks were manufactured at Technicrete’s White River plant to a thickness of 220mm, as opposed to the standard Armorflex thickness of 115mm.
Individual blocks were then “laced” together with polyrene, a rope made from a particularly strong chafe-resistant mix of polyster and nylon. Each mat consists of 152 blocks and weighs 5,8 tons. Measuring 5,9m X 2,4m, the mats were assembled in White River and transported to Mozambique on flat bed trucks.
Taco Voogt, Technicrete product development manager, says: “It’s very important that each mattress is correctly laid to fit snugly against its neighbour to ensure maximum effect.”
The area where the mats were laid is extremely muddy and so it was not considered advisable to use divers. “Laying all mats individually means performing the same operation 240 times without the aid of divers – a very time-consuming exercise. Therefore the possibility was investigated of linking the mats together to form bigger units, which could be laid in a limited number of operations.”
To join the mats together, four half blocks were left out on each side so that rebar could be threaded through end-loops protruding from the mats.
The blocks were duly built and the mats assembled and deployed, resulting in improved conditions in Beira port.
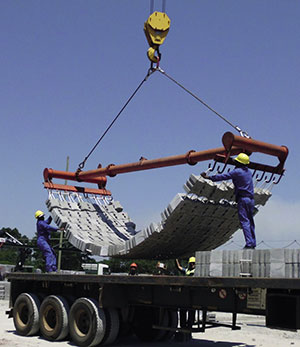
Technicrete Armorflex blocks
|